Marine is where C-Tech began — and where we continue to lead.
From our founder hand-building carbon spars for skiffs to supporting every America’s Cup campaign since 2003 — our story started on the water and has grown with the sport. Today, our composites power everything from Moths and offshore racers to superyachts, cruising yachts, and support craft.
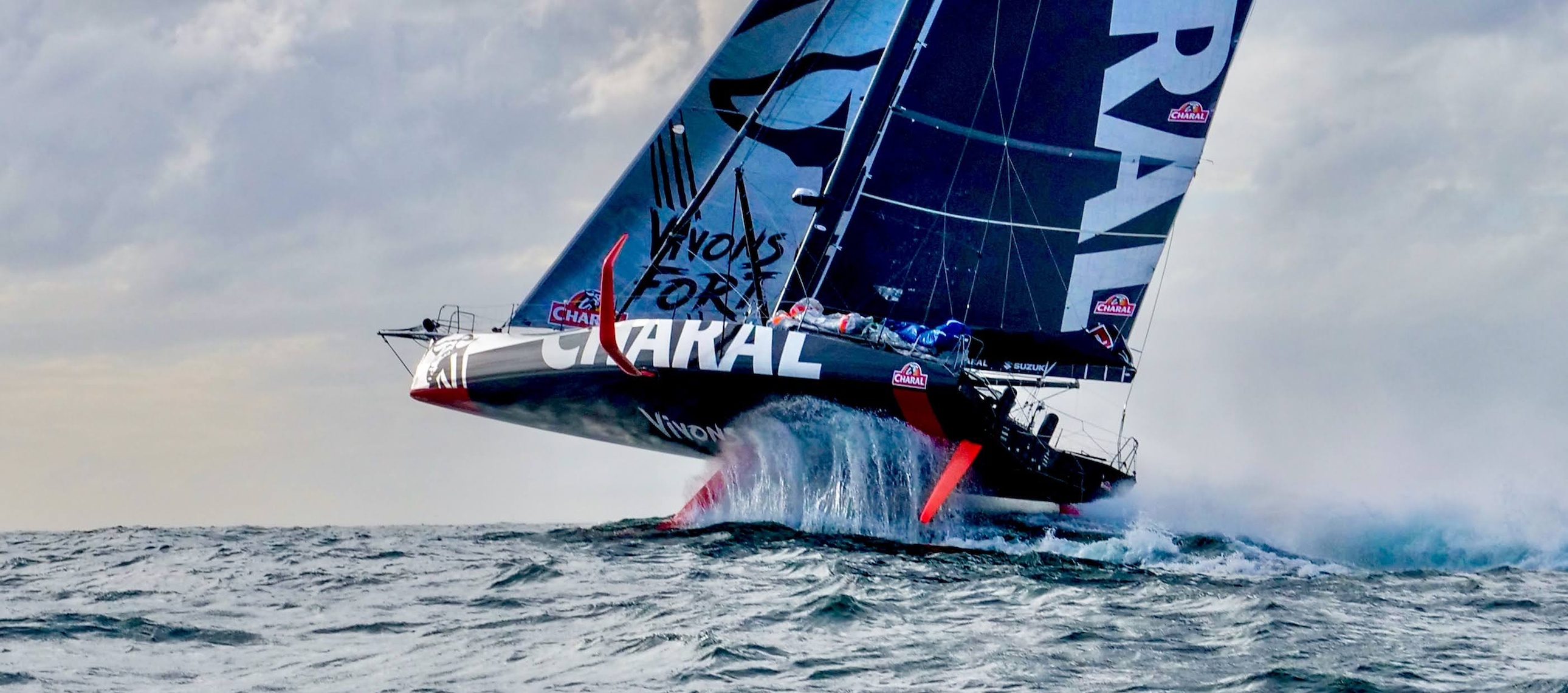
With 28+ years experience in carbon fibre composites, C-Tech is trusted by the world’s top to deliver strength, precision, and performance in the harshest conditions. It’s not just what we do — it’s who we are.
Trusted by world-class industries.
Built for marine.
We're not new to performance at sea.
Backed by 28 years of experience in elite sailing and marine innovation, C-Tech delivers carbon fibre components proven in the most demanding conditions — from battens and spars to structural tubes and custom components built to perform at sea.
Of experience in high-performance composite manufacturing.
Across defence, America’s Cup, and space exploration.
We are comfortable working in microns and can meet tolerances from as small as 0.05mm.
Backed by Champions
Trusted by Industry
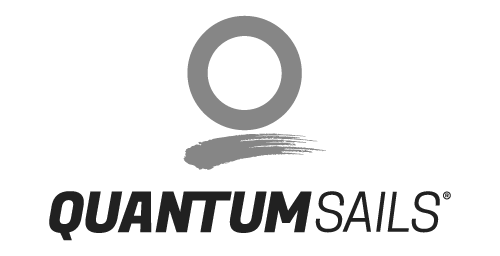
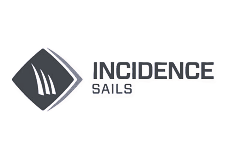
From problem — to innovative solution.
We collaborate with you at every stage of the process. Our engineering team is hands-on from start to finish from early-stage solution design to prototyping, refining layups, and debugging production issues.
We work along side marine engineers and system designers to solving real challenges building integrated marine capability solutions.
We don't just manufacture.
We innovate.
Every component is engineered in-house, proven on the water, and trusted to perform.
From battens to foils, we rethink, refine, and push the limits of marine performance — delivering smarter, faster, stronger solutions that give teams the edge.
Spars
Marine Spars.
Built to Perform.
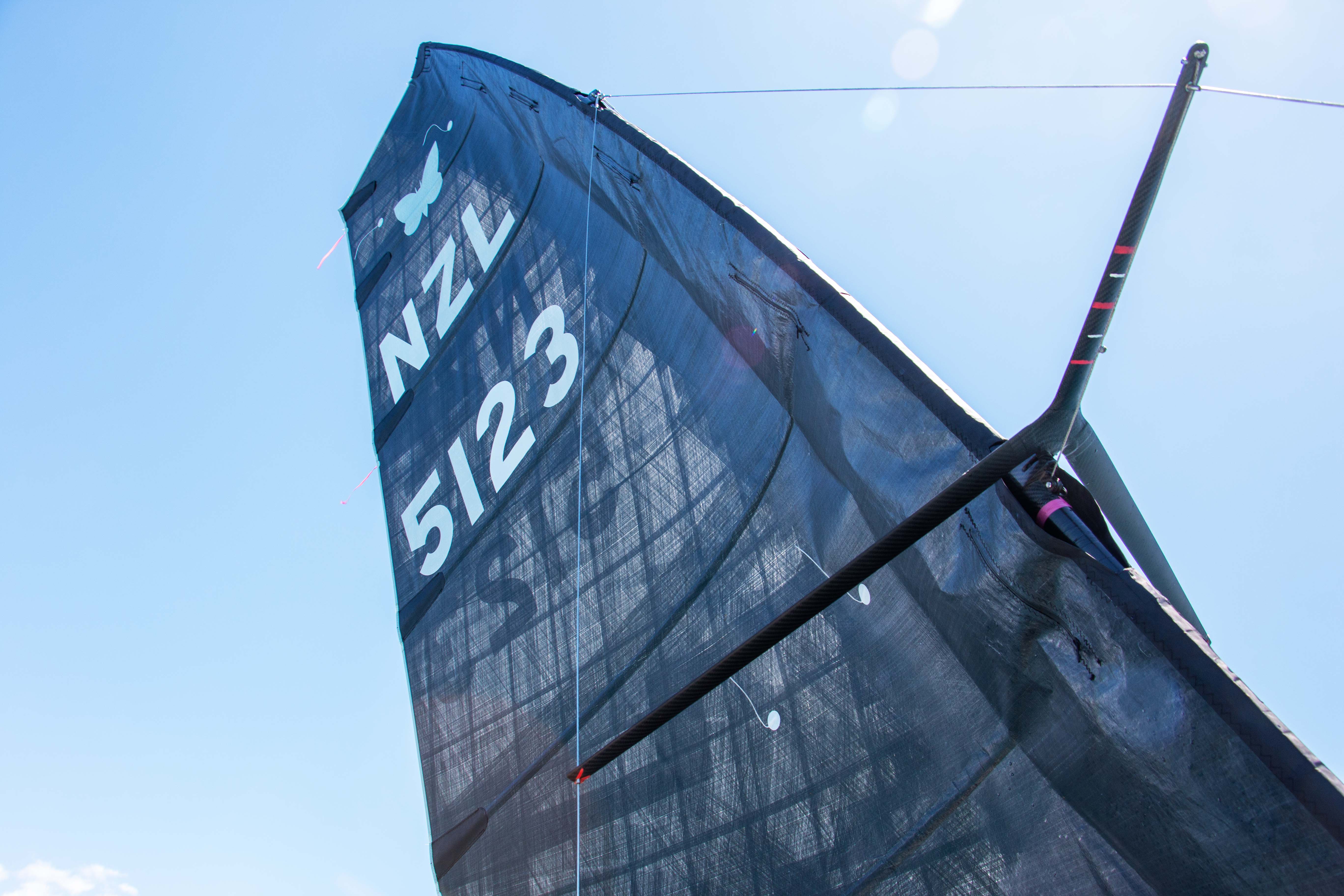
C-Tech marine spars are trusted by sailors and boatbuilders around the world — from foiling dinghy fleets to offshore racing yachts and performance superyachts. All our spars are custom-built using high-modulus prepreg carbon fibre, precision laminate placement, and autoclave consolidation to achieve maximum strength, durability, and bend requirements.
Our marine spar products include:
Carbon Masts & Booms
Lightweight, stiff, and tailored to class specs and load profiles.
Spinnaker Poles & Prods
Designed for easy handling and responsive control under pressure.
Reaching Struts & Jockey Poles
Strong, dependable, and built to meet the unique geometry of each boat
Whether you're chasing marginal gains in a skiff or dinghy, needing bulletproof hardware, or speccing a custom solution for a performance multihull or superyacht, C-Tech spars deliver performance you can rely on — race after race, mile after mile.
Battens & Hardware
Built for the Sail, Designed for Performance.
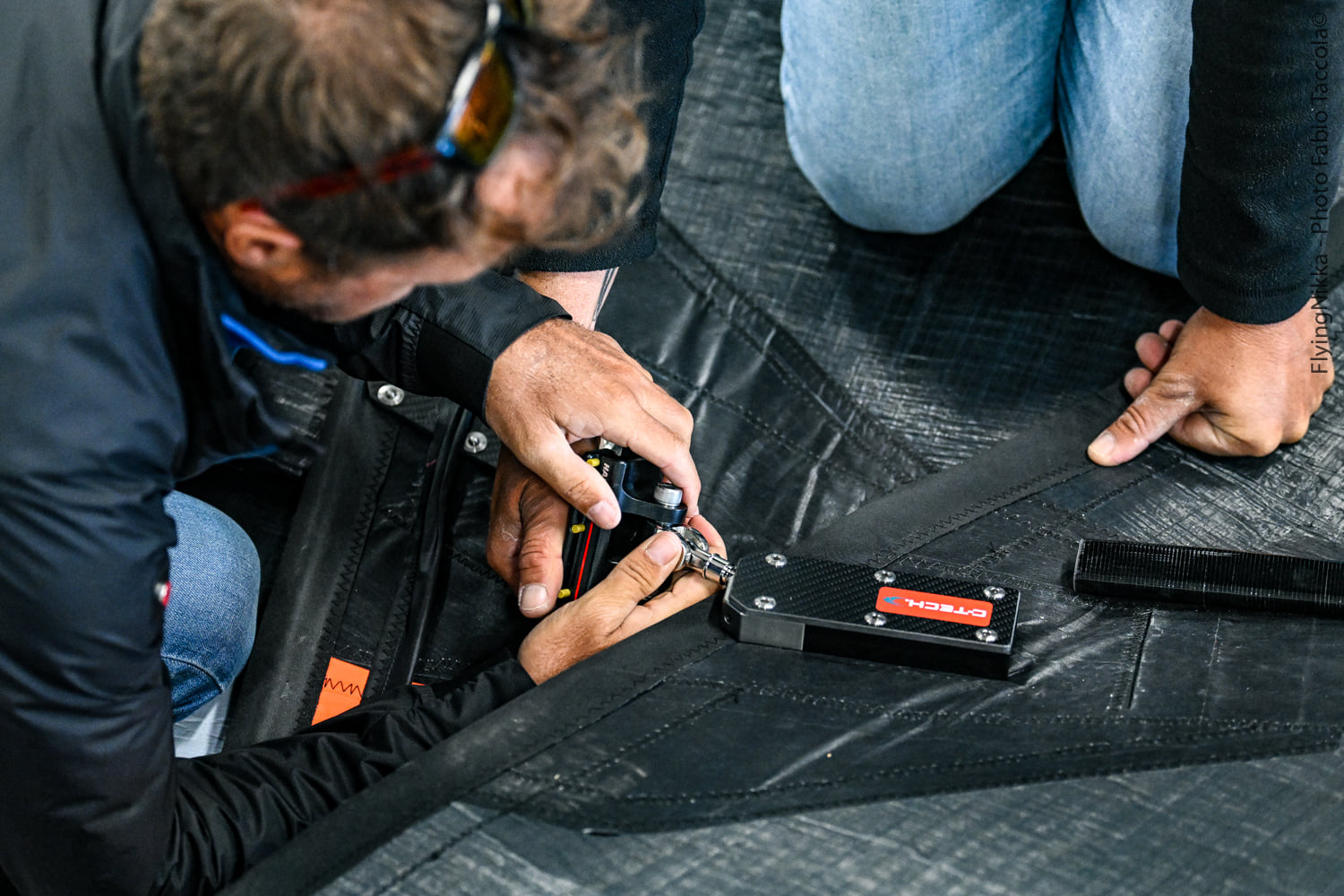
Behind every fast, reliable sail is a batten system doing the heavy lifting — and for over 30 years, C-Tech has been the leading supplier trusted by America’s Cup teams, offshore campaigns, sailmakers, and classes around the world.
Whether you’re chasing every ounce of performance in an 18ft skiff, relying on durability and speed in an IMOCA across the Southern Ocean, or looking for low-maintenance ease on your cruising cat — every C-Tech batten is custom-built to meet your boat, sail, and spec.
Our range includes:
Solid Plate Battens
For dinghy classes, Moths, and jibs where space and stiffness are key.
Hollow Tube Battens
From CT22s for 30-footers up to CT40s for 200ft+ superyachts — precision-tuned for flex and loaded performance.
FlexiFurl Battens
Designed specifically for furling sails, with smooth transitions and reliable furl compatibility.
Hardware Systems
Luff and leech end fittings, clewboards, custom batten receptacles and compression hardware — all engineered for long-term repeat use and high load cycles.
SnuffAir Inflatable Snuffers
Lightweight, compact, and robust solutions for safe spinnaker takedowns — adaptable to any yacht
We engineer battens around your sail designs and unique requirements. Our long-standing partnerships with top lofts and race teams, including America’s Cup teams, feed directly into the constant evolution of our products. From materials to moulding to fitting technology, our hardware and battens stay ahead — and bring that advantage to every boat we touch.
Custom Components
Custom Components — Built for Purpose
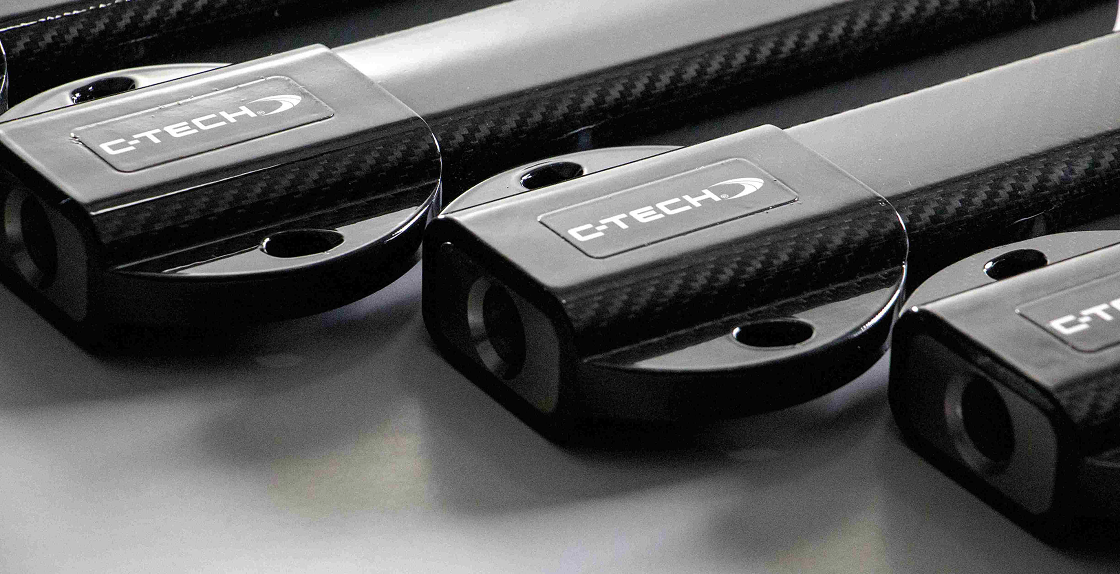
C-Tech engineers and manufactures precision custom carbon fibre components for elite marine applications. Our team works closely with designers, engineers, and race teams to develop lightweight, high-strength solutions tailored to exact project specifications. Examples of some custom components include:
America’s Cup control systems
Engineered for maximum reliability and exacting tolerances
Carbon dashboards and panels
Lightweight, stiff, and designed for superyachts and recreational launches
Waterproof camera housings
Fully custom, rugged enclosures built for marine conditions
Whether it’s a single one-off or a complex integrated system, we provide composites built to perform, endure, and impress.
Marine Tubes
Marine Tubes — Engineered for Strength and Precision
.jpg)
C-Tech specialises in producing marine-grade carbon fibre tubes made to order for a wide range of high-load and structural marine uses. Using roll-wrapped prepreg and autoclave curing, each tube achieves optimal fibre alignment, minimal void content, and excellent stiffness-to-weight ratios.
Our custom tubes often become critical components in:
Compression struts and accumulator cylinders designed to withstand high loads
Tuna tower frameworks and foldable chaseboat masts crafted for strength and corrosion resistance
Superyacht awnings, stanchions, swim ladder tubes, and telescopic masts requiring precision and durability
Tender fender tubes and other specialised marine assemblies tailored to project requirements
We collaborate closely with designers and builders to deliver tubes engineered exactly to the specs and demands of your marine build — whether for racing, commercial, or recreational vessels.
Foils
High-Stiffness Foils & Reinforcements
Engineered for elite-level performance — built to withstand the forces of high-speed foiling and offshore racing.
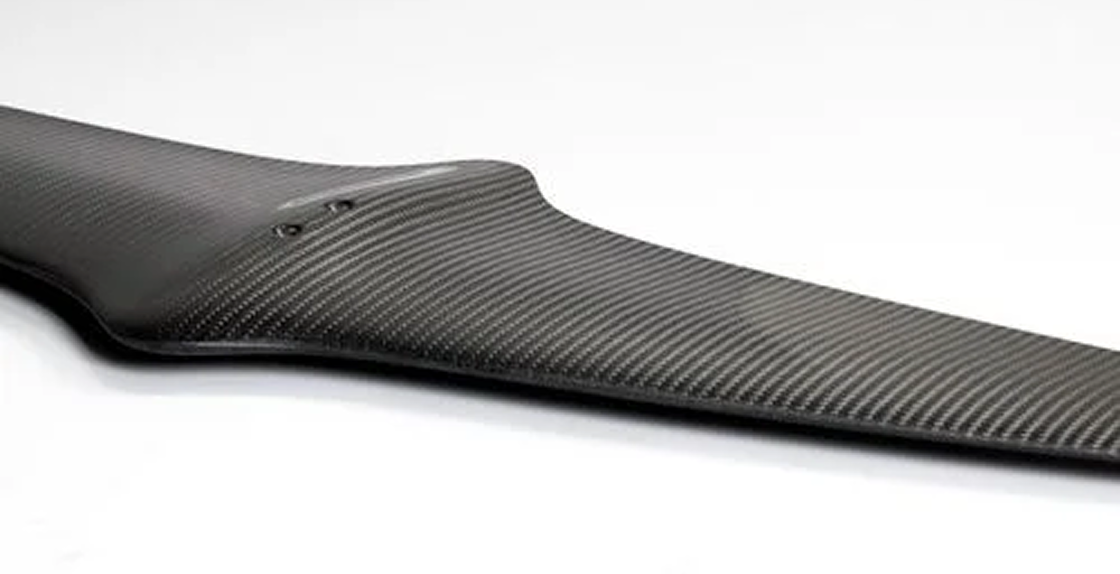
Using prepreg carbon fibre, precision moulding, and autoclave curing, our components are manufactured for extreme loads, low drag, and tight dimensional tolerances. We specialise in large or repeatable foil projects where consistency, accuracy, and performance are critical.
Whether it's:
Production-run high performance one-design foils for SailGP or the International Moth class
Custom lifting foils, canards, and reinforcement structures
Rudders and rudder stocks for offshore racing and high-performance yachts
We partner with you to deliver tailored solutions that meet your structural loads, weight targets, and hydrodynamic goals. These are not off-the-shelf dinghy components — they’re performance-grade systems built for serious speed.
America’s Cup
Aerodynamic Systems Built to Perform Under Pressure
Precision composite engineering honed in elite sailing — now applied to UAVs, missile platforms, and aerodynamic defence systems.
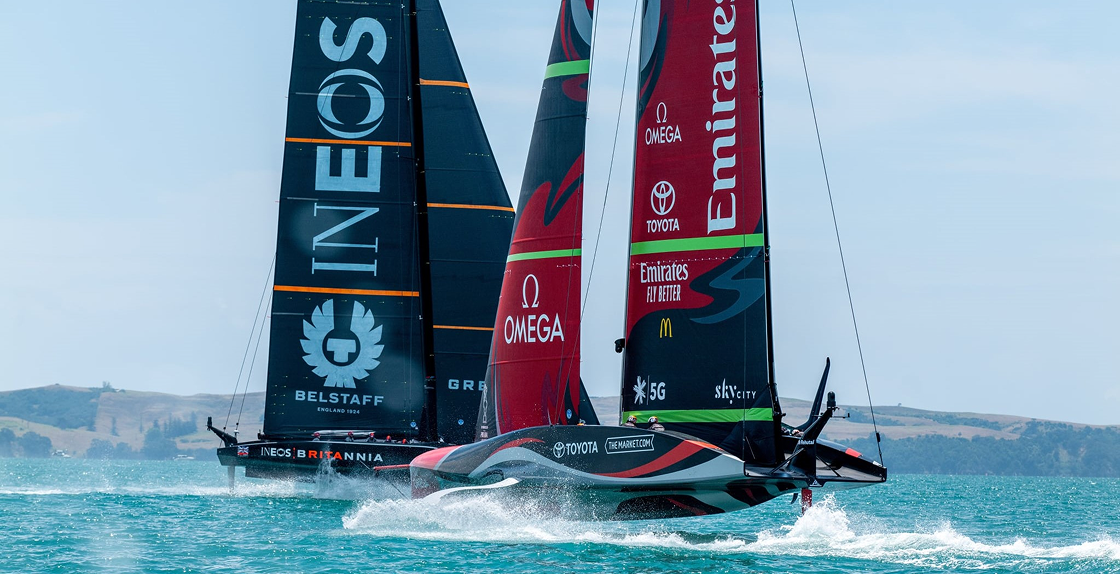
C-Tech supplied carbon fibre components to multiple America’s Cup teams, including foils, wings, and load-bearing structures. These ultra-light, fatigue-resistant components were engineered for speed, control, and aerodynamic efficiency — the same principles that now underpin our work on defence-grade UAV fuselages, control arms, and loitering munitions.
Wireline Logging
Built for Harsh Environments. Trusted to Protect Payloads.
Originally developed for geophysical sensor systems, these ruggedised carbon fibre tubes now support defence field tech and mobile surveillance applications.
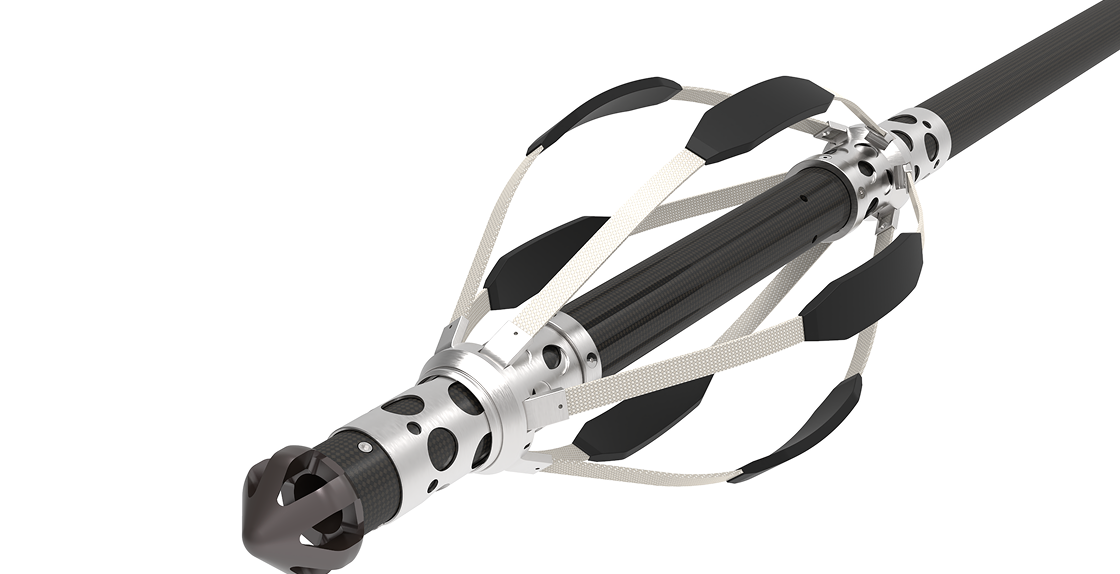
Designed for the oil and gas sector, our wireline tubes withstand shock, vibration, and repeated mechanical load in extreme terrain. With precision-machined interfaces and proven fatigue resistance, these tubes now serve as structural enclosures for tactical communications, field-deployable sensors, and ruggedised defence payloads.
Ice Drill
Modular Strength for Expeditionary and Recon Platforms
Engineered for lightweight performance in polar expeditions, our modular tube systems are ideal for mobile, mission-critical defence systems.
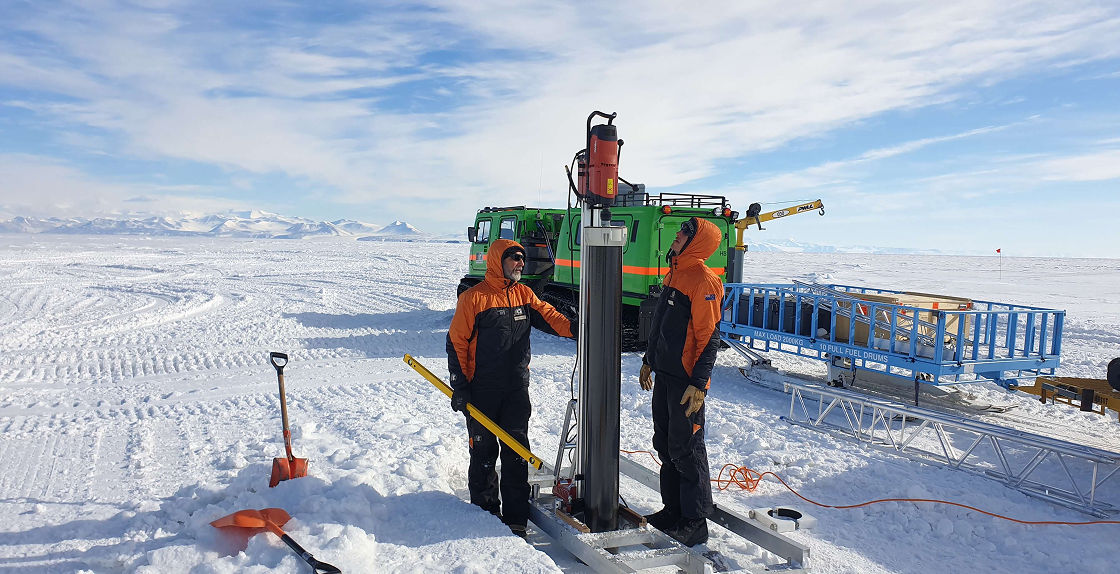
Developed for deep ice drilling missions in Antarctica, this modular carbon fibre drill string was designed for easy field transport and high axial strength. These same capabilities make it ideal for military recon equipment, portable antenna masts, or remote field systems — anywhere ultra-light, strong, and field-assembled components are needed.
Telescopic Comms Tubes
Deployable Carbon Fibre Tubes for Tactical Comms & ISR
Large-diameter carbon tubes custom-built for defence clients needing fast-deploy, corrosion-resistant comms infrastructure.
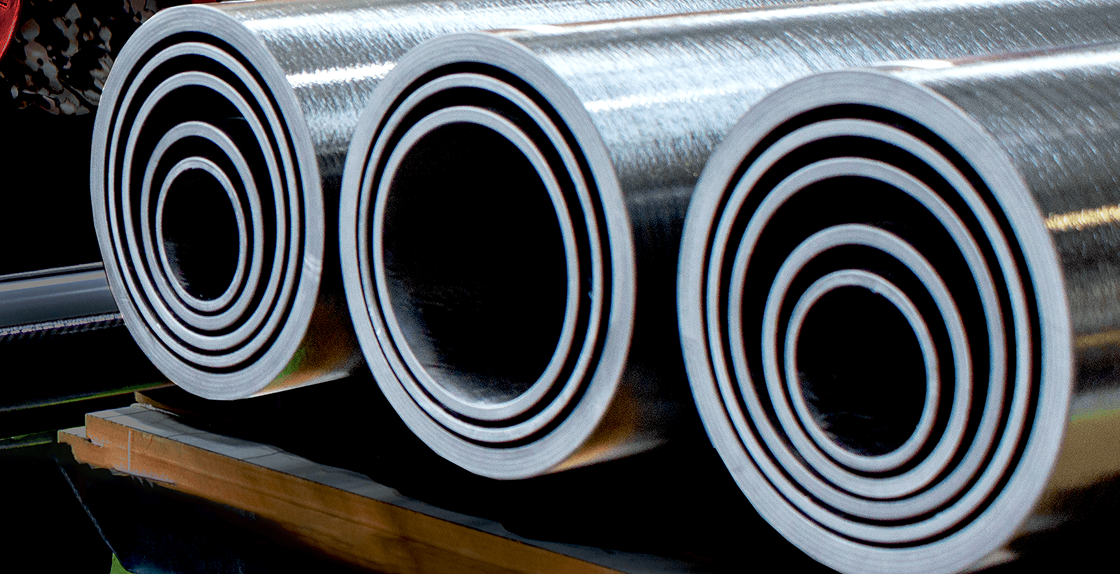
These telescopic carbon fibre systems are used to deploy antennas, radar equipment, and mobile surveillance gear in operational defence environments. With custom interface design, high stiffness, and rapid extension/retraction features, they provide reliable performance in field communications, observation, and tactical command systems.
Because Performance
Demands Precision.
At C-Tech, every part we make is built to perform —engineered with precision, tested for strength, and trusted in the world’s most demanding environments.
Every part is designed and engineered in-house, allowing full traceability and control — from fibre orientation and layup sequences to curing cycles and final inspection.
This isn’t just about making parts that last. It’s about delivering the exact performance profile you need, every time.
From custom foils and structural tubes to sail hardware built to survive the Southern Ocean — we solve performance challenges with a deep understanding of the loads, flex profiles, and marine dynamics our customers face.
Local Reliability.
Performance in Field.
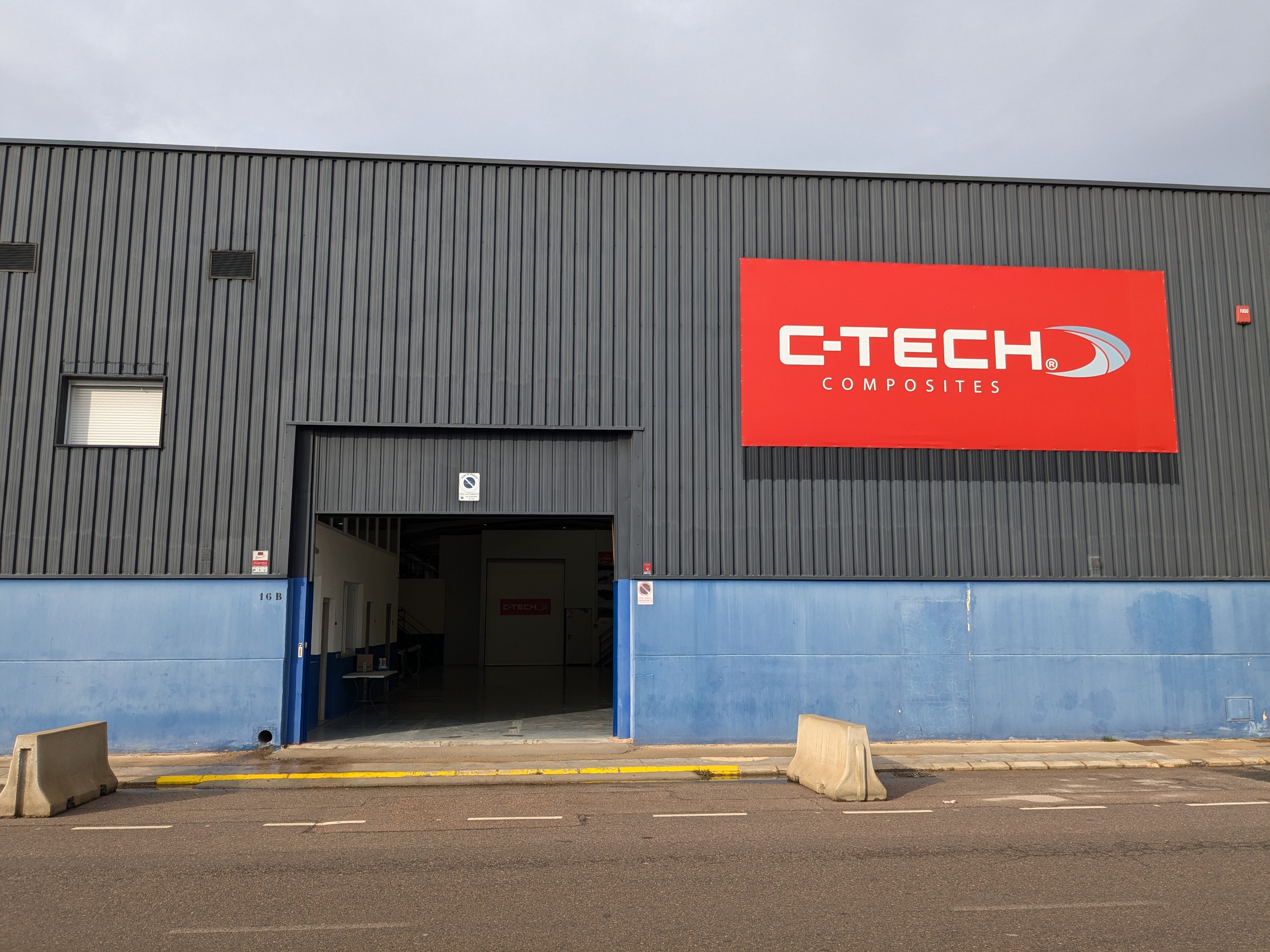
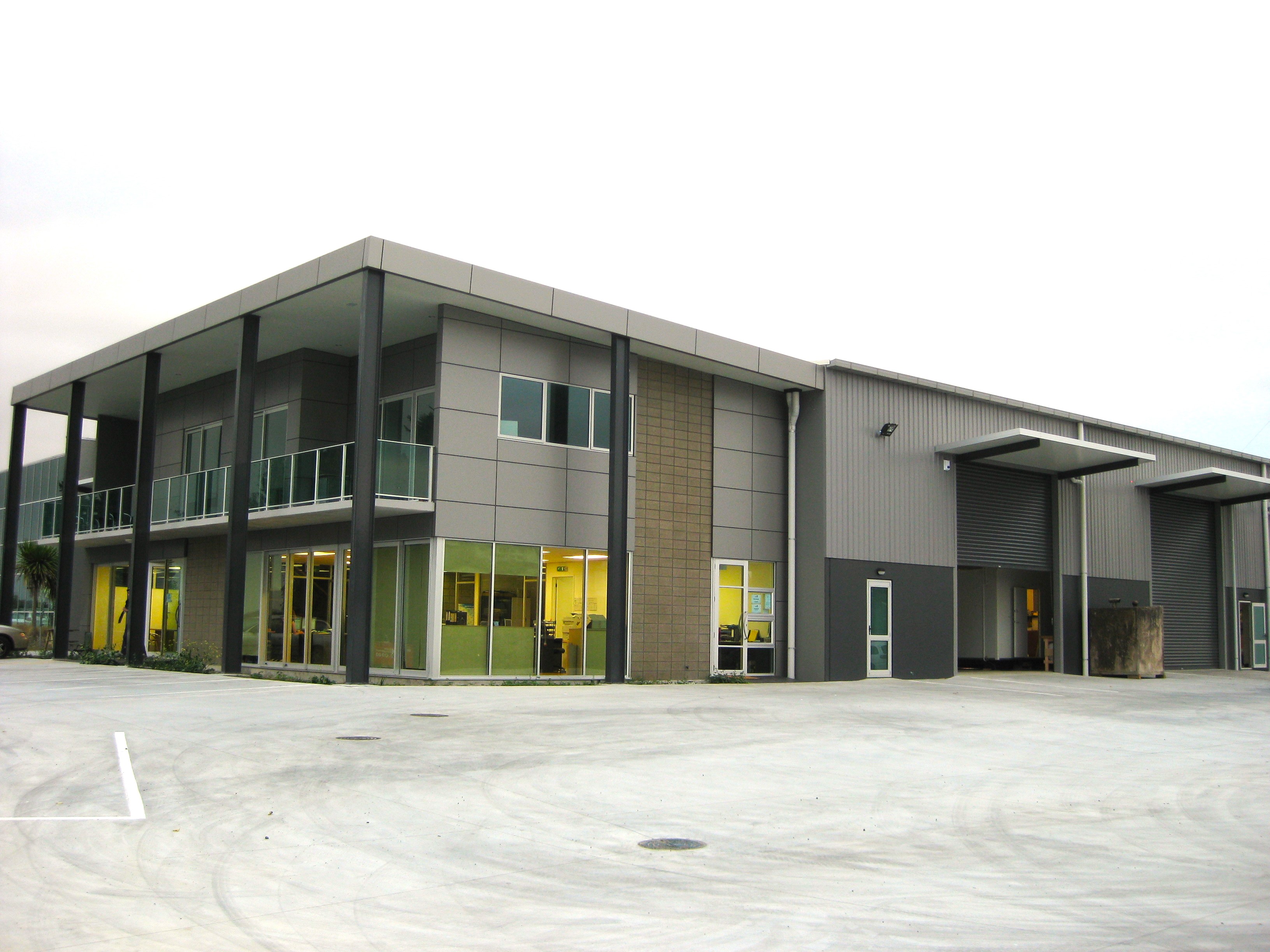
Trusted by Experts
We collaborate with the world’s best sailmakers, designers, and teams, and we’re proud to be a trusted supplier across every major discipline in the sport.
Cesar Dohy
John Parker, GBR
Dougall Love
Rig Construction Coordinator
Gautier Sergent, Head of R&D
Sail Loft Manager
Christen, Norway
How carbon enables better
solutions for marine.
Carbon fibre outperforms traditional materials where it matters most. Our composites are lighter, stronger, more resilient — and engineered for the demands of real-world marine environments.
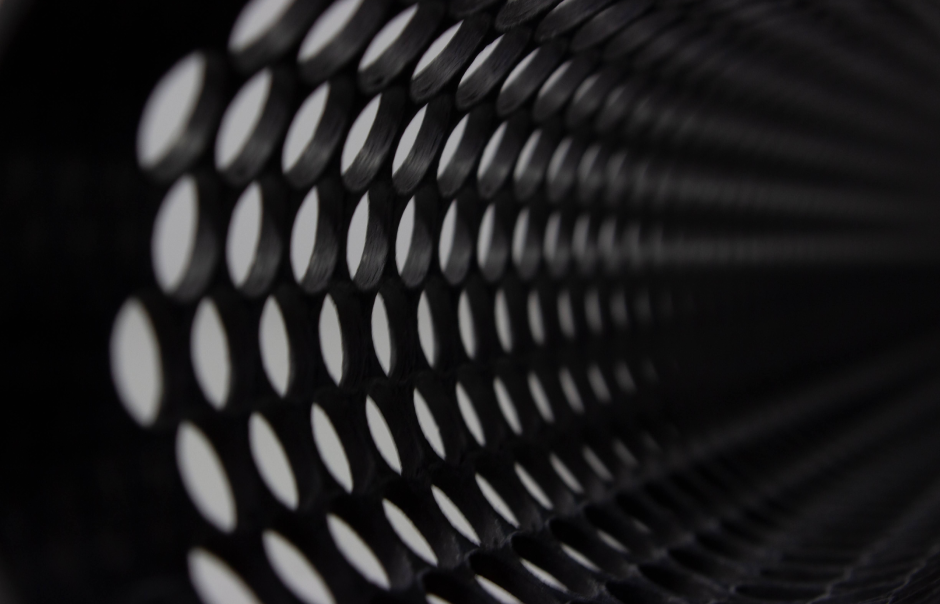
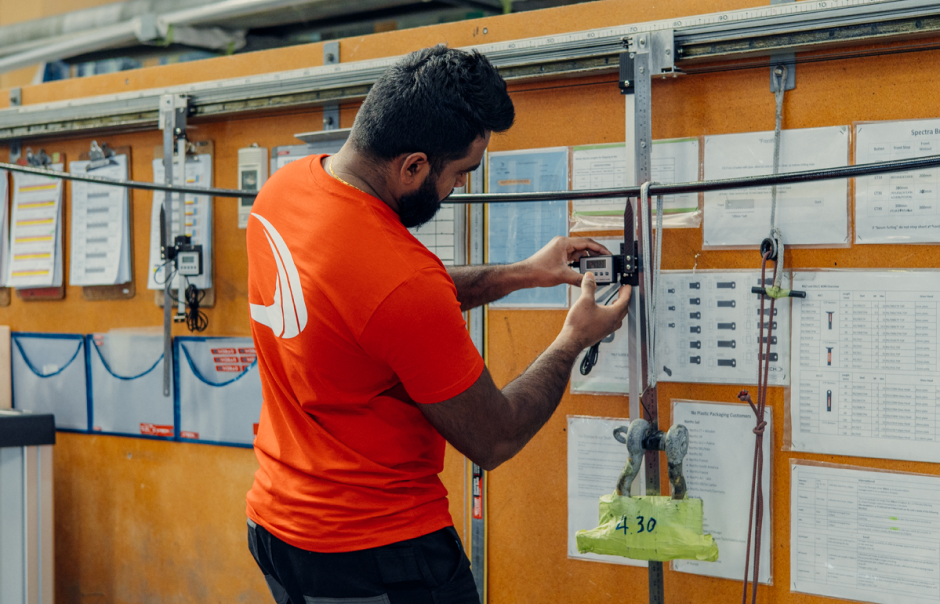
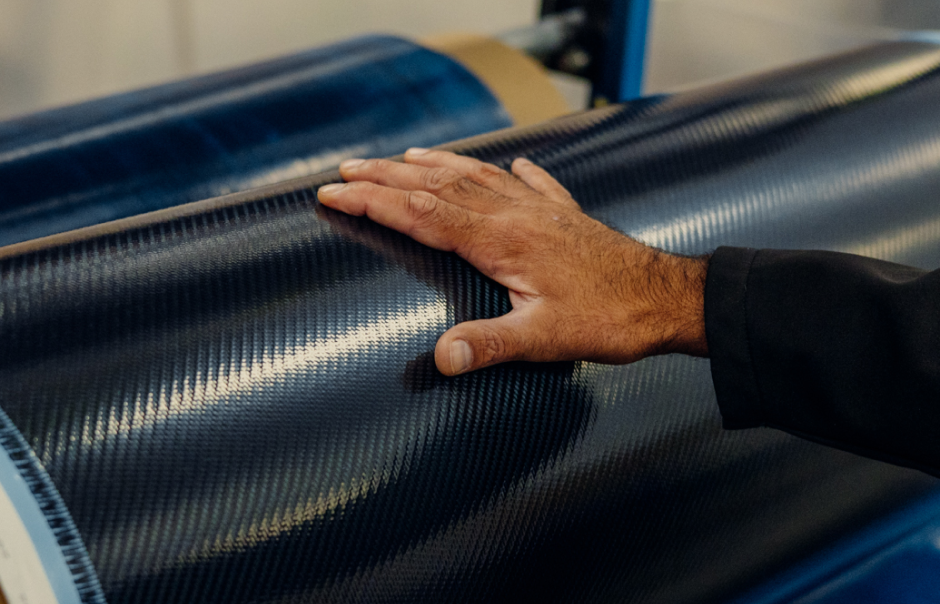
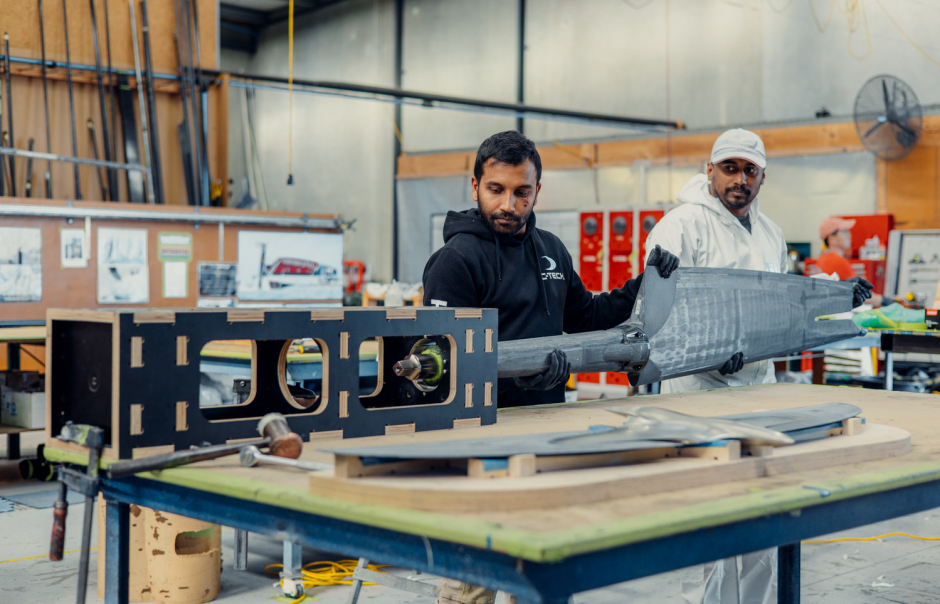
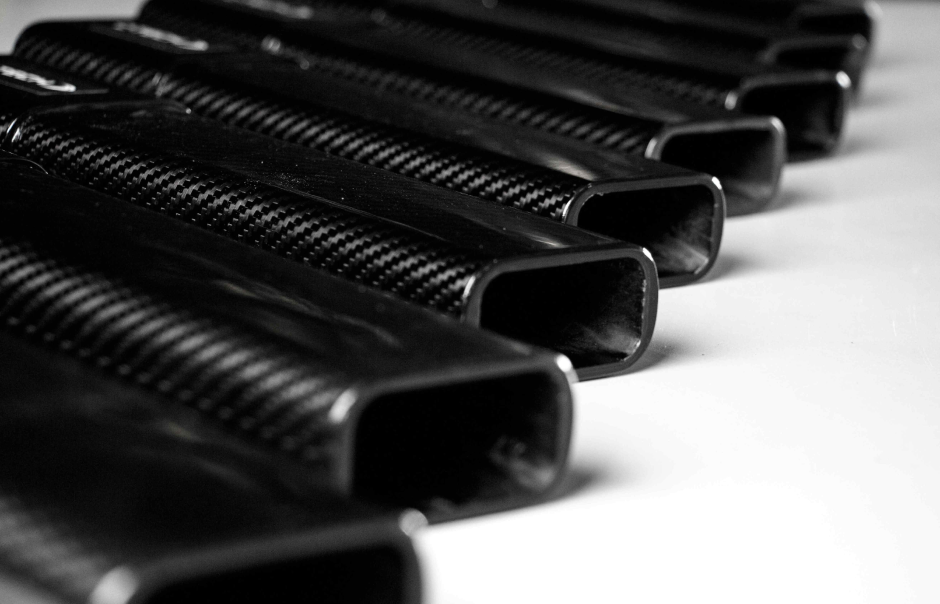
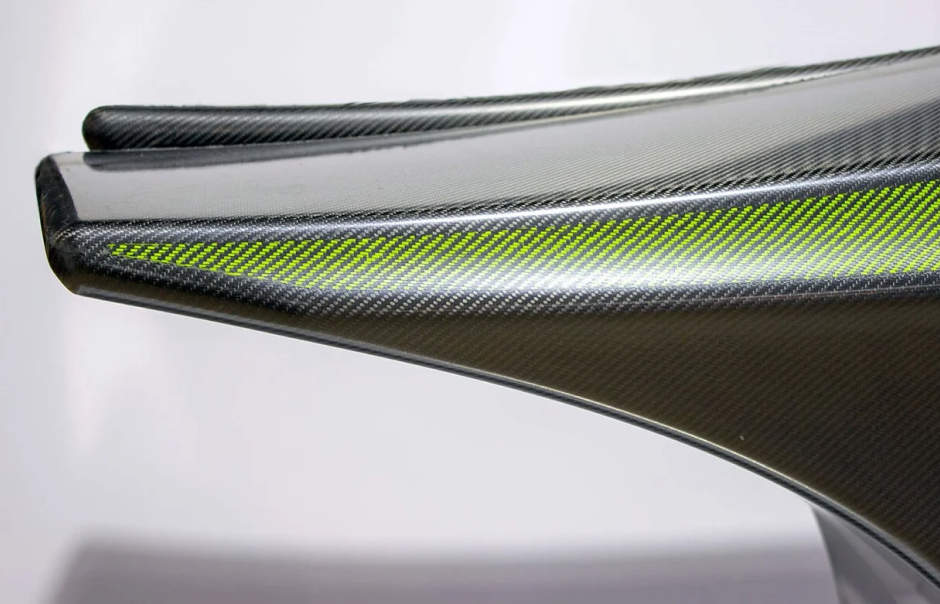
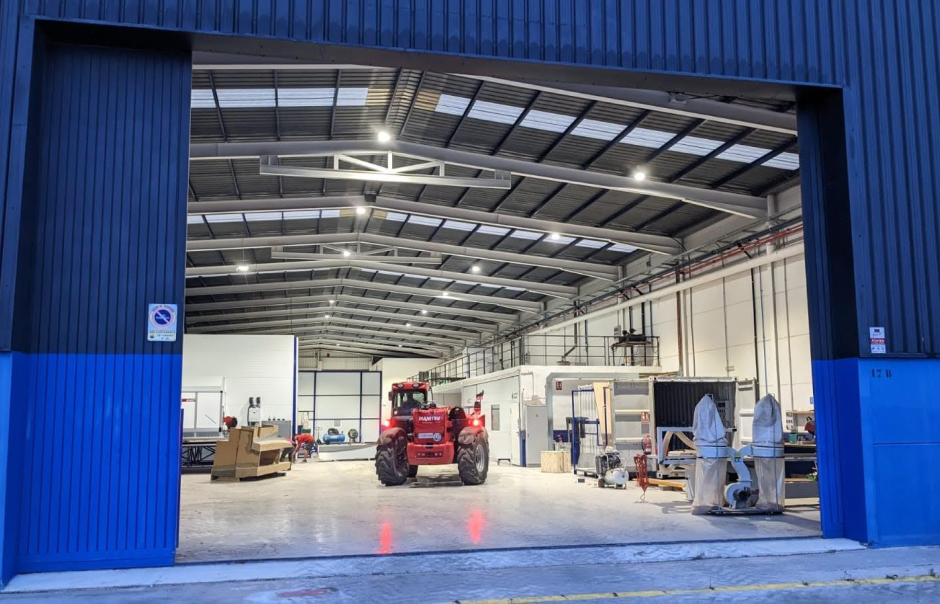
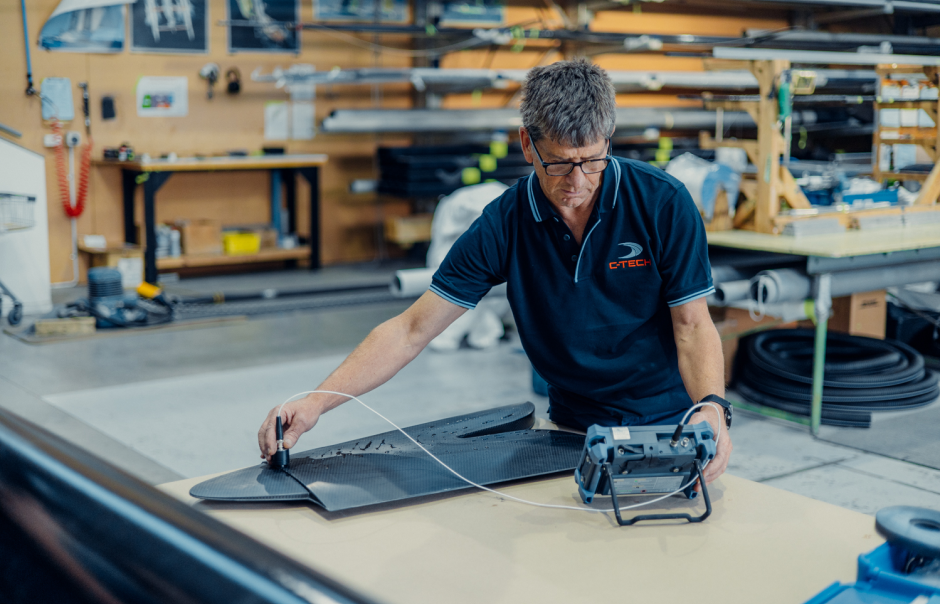
Schedule Your Marine Project Consultation
C-Tech. Engineered Precision. Proven Offshore.